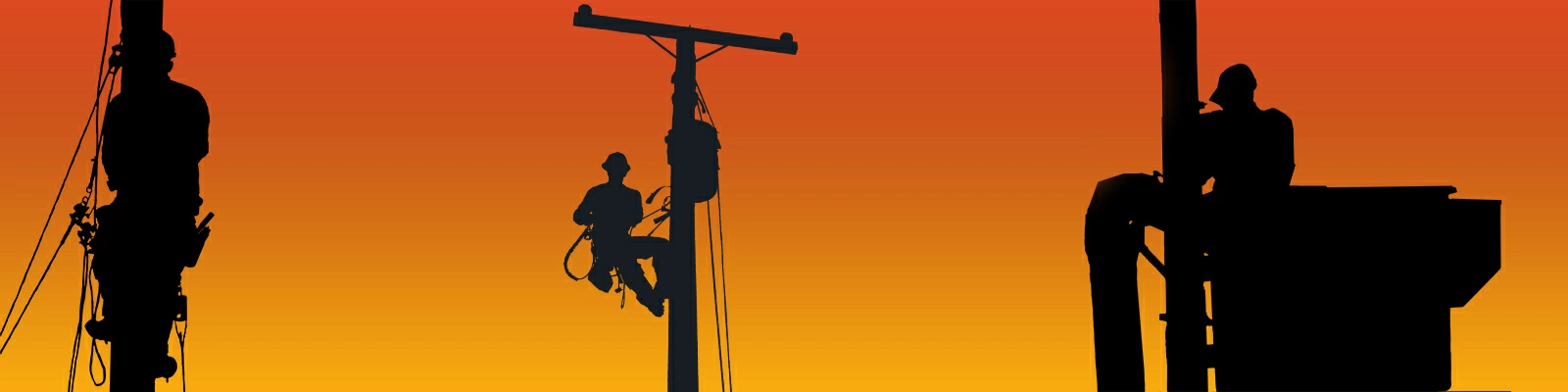
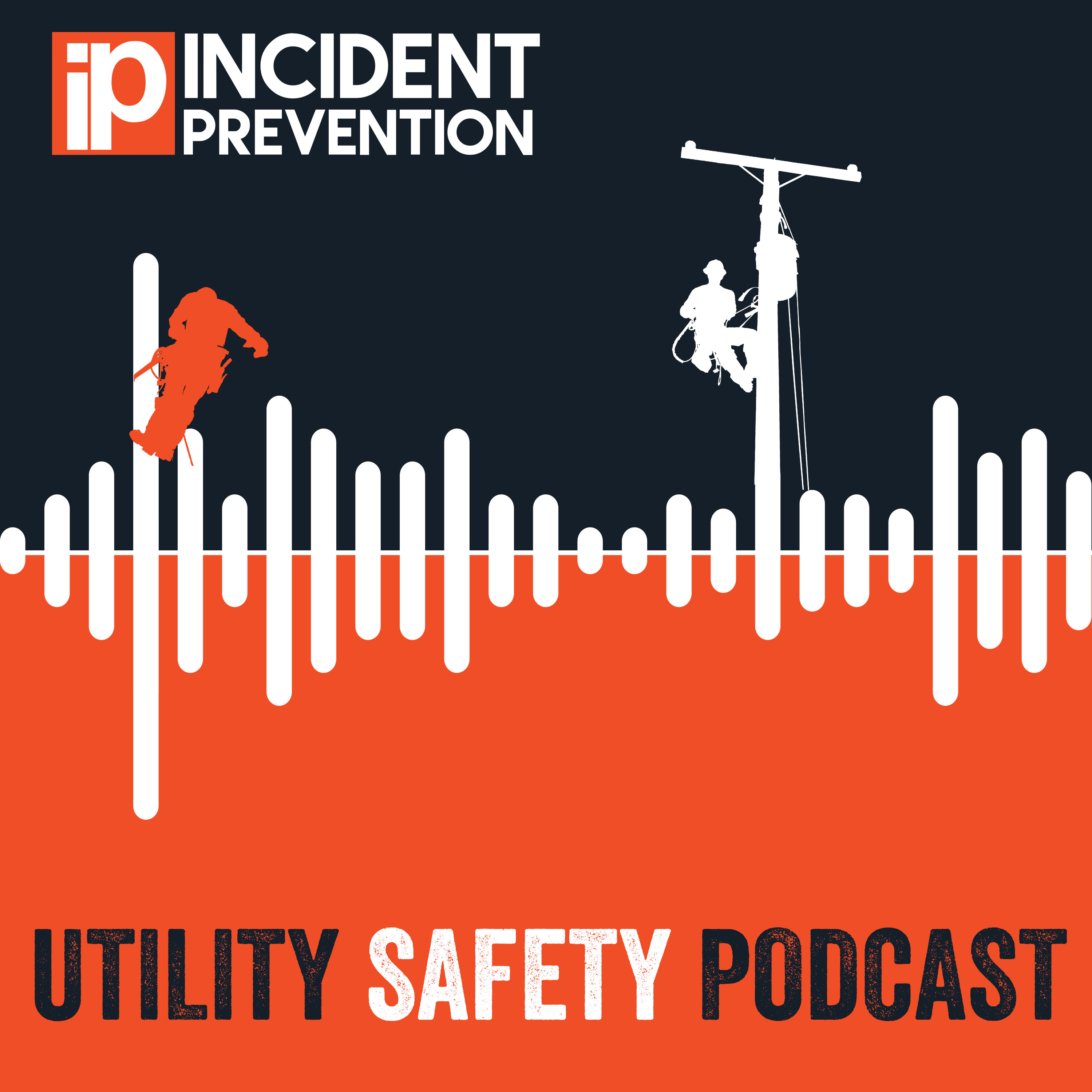
25K
Downloads
112
Episodes
Come listen to an extension of some of the excellent utility safety & ops safety content published in Incident Prevention magazine. Dive deeper into insightful safety topics by hearing interviews with the some of the best and brightest minds in the industry! Learn more about Incident Prevention magazine at incident-prevention.com
Episodes
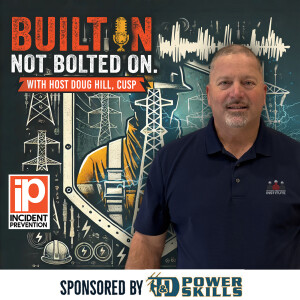
Thursday May 01, 2025
Thursday May 01, 2025
In this episode of Built In, Not Bolted On, host Doug Hill sits down with safety leader and educator David McPeak to explore the real keys to successful Human and Organizational Performance (HOP). Through storytelling, relatable analogies, and a few laughs, they break down the power of caring leadership, building a just culture, the dangers of overcomplicating safety systems, and the importance of embedding safety into the DNA of an organization. From tools like “E + R = O” to the “village-by-village” model of influence, this episode provides a practical, people-first look at how to make safety initiatives stick—for good.
🔑 Key Takeaways:
-
Culture eats strategy for breakfast. Safety systems must be embedded into the culture—not simply bolted on as compliance requirements.
-
Toxic culture is a showstopper. No safety program will succeed in an environment that lacks trust, respect, and accountability.
-
Success starts with relationships. Building strong, caring teams helps create the psychological safety needed to speak up and improve performance.
-
Don’t overcomplicate safety. Practical, repeatable tools that workers understand and use in context matter more than complex policies.
-
Peer-level champions and simple tools like “E + R = O” and performance mode awareness can drive real change from the ground up.
5 Relevant Questions & Answers:
Q1: What’s the key to implementing effective Human and Organizational Performance (HOP) strategies?
A1: Commitment and time. It’s not about quick fixes—it’s about embedding care, consistency, and communication into every level of the organization.
Q2: Why do many safety programs fail?
A2: They’re often implemented in toxic cultures or made too complex. Without foundational trust and simple, relatable tools, programs won’t stick.
Q3: How can you tell if a safety initiative is “built in” versus “bolted on”?
A3: “Built-in” programs are part of daily work, language, and habits. “Bolted-on” programs feel forced, top-down, and are quickly abandoned.
Q4: What role do performance modes play in safety?
A4: Understanding if a worker is in skill-, rule-, or knowledge-based mode helps choose the right tool—like saying it out loud, step-by-step checks, or stopping work to seek help.
Q5: How can leaders support cultural safety transformation?
A5: By modeling desired behaviors, creating a safe space for feedback, understanding how each role sees safety, and helping translate tools into all departments—not just field crews.
#BuiltInNotBoltedOn #UtilitySafety #HumanPerformance #SafetyCulture
#OrganizationalLeadership #JustCulture
Contact Doug: doug@utilitybusinessmedia.com
Subscribe to Incident Prevention Magazine - https://incident-prevention.com/subscribe-now/
Register for the iP Utility Safety Conference & Expo - https://utilitysafetyconference.com/
________________________________
This podcast is sponsored by T&D Powerskills. If you are looking for a comprehensive lineworker training solution, visit tdpowerskills.com today and use the exclusive podcast listener promo code IP2025 to receive a 5% discount!
No comments yet. Be the first to say something!